Keep Your Line Running Smoothly with Reliable Packaging Machine Repair
Keep Your Line Running Smoothly with Reliable Packaging Machine Repair
Blog Article
Quick and Reliable Product Packaging Maker Repair Work Services to Lessen Downtime
In the affordable landscape of production, the efficiency of packaging procedures pivots on the integrity of machinery. Quick and reputable repair work services are crucial in mitigating downtime, which can lead to significant functional setbacks and financial losses.
Value of Timely Services
Prompt fixings of product packaging equipments are critical for keeping functional performance and lessening downtime. In the hectic atmosphere of production and packaging, even small breakdowns can cause considerable delays and productivity losses. Addressing concerns without delay makes sure that makers operate at their optimal ability, consequently securing the flow of procedures.
In addition, routine and timely maintenance can prevent the acceleration of minor troubles right into major breakdowns, which usually sustain higher fixing expenses and longer downtimes. A proactive strategy to maker repair work not just protects the integrity of the tools however additionally improves the overall integrity of the assembly line.
In addition, timely fixings contribute to the long life of packaging machinery. Equipments that are serviced promptly are much less most likely to suffer from too much deterioration, permitting services to optimize their investments. This is specifically essential in sectors where high-speed packaging is crucial, as the requirement for regular performance is vital.
Benefits of Reliable Company
Trustworthy provider play a crucial role in making sure the smooth procedure of packaging makers. Their expertise not only improves the performance of repair work however additionally contributes considerably to the durability of tools. Dependable company are outfitted with the technical knowledge and experience needed to detect concerns accurately and implement efficient options promptly. This lowers the threat of recurring problems and guarantees that makers run at ideal efficiency degrees.
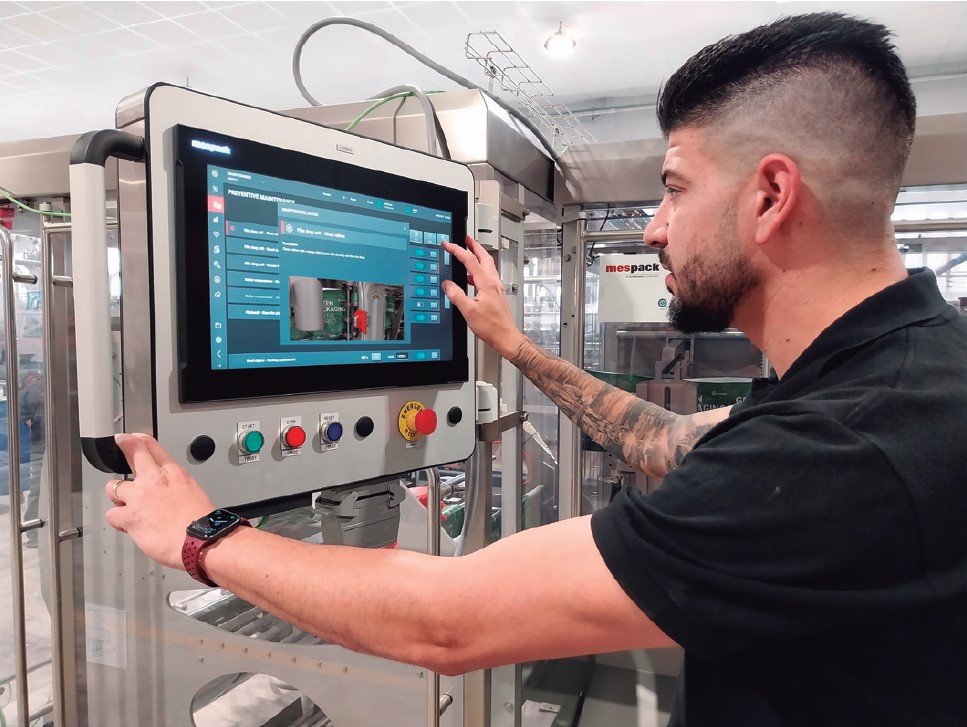
In addition, a trustworthy company supplies thorough assistance, consisting of training and support for personnel on device operation and maintenance ideal practices. This not only empowers staff members yet likewise cultivates a culture of safety and performance within the company. Generally, the benefits of involving trusted company extend beyond prompt repair services, positively impacting the whole operational workflow of product packaging processes.
Common Product Packaging Device Issues
In the world of packaging operations, numerous issues can jeopardize the performance and performance of equipments (packaging machine repair). An additional typical concern is misalignment, which can trigger jams and irregular product packaging, impacting item top quality and throughput.
Electric troubles can also interfere with product packaging operations. Malfunctioning wiring or malfunctioning sensors might cause erratic device habits, creating delays and enhanced functional prices. In addition, software glitches can impede the maker's shows, leading to operational ineffectiveness.
Irregular item circulation is an additional critical issue. This can occur from variations in product weight, form, or size, which may impact the device's capability to manage products properly. Ultimately, not enough training of drivers can aggravate these troubles, as inexperienced employees might not acknowledge early indications of malfunction or may misuse the equipment.
Dealing with these common packaging machine concerns immediately is important to preserving efficiency and guaranteeing a smooth operation. Normal assessments and positive maintenance can significantly minimize these worries, promoting a dependable product packaging setting.
Tips for Lessening Downtime
To reduce downtime in product packaging procedures, executing an aggressive upkeep strategy is critical. Consistently arranged upkeep checks can determine potential concerns before they rise, making sure machines operate successfully. Developing a regimen that includes lubrication, calibration, and assessment of important parts can substantially decrease the regularity of unexpected failures.
Educating staff to run equipment properly and identify early indication of breakdown can likewise play an essential function. Encouraging operators with the understanding to execute fundamental troubleshooting can protect against minor concerns from causing significant hold-ups. Keeping a well-organized inventory of necessary extra components can expedite repair work, as waiting for components can lead to prolonged downtime.
Furthermore, recording maker efficiency and maintenance activities can help determine patterns and recurring problems, enabling targeted interventions. Integrating innovative surveillance technologies can offer real-time data, allowing anticipating upkeep and lessening the danger of abrupt failings.
Last but not least, cultivating open interaction in between drivers and upkeep groups makes certain that any type of abnormalities are without delay reported and resolved. By taking these aggressive actions, organizations can boost operational performance and significantly reduce downtime in packaging procedures.
Picking the Right Fixing Solution
Choosing the suitable repair work service for packaging equipments is a critical choice that can substantially impact operational performance. An appropriate company ensures discover here that your equipment is fixed swiftly, effectively, and to the highest possible criteria. Begin by assessing the company's experience with your particular sort of product packaging equipment. A technician aware of your equipment can identify issues extra precisely and implement remedies a lot more quickly.
Next, take into consideration the provider's credibility. Looking for feedback from various other organizations within your market can provide understandings into dependability and quality. Accreditations and collaborations with recognized equipment manufacturers can additionally suggest a commitment to quality.
Additionally, examine their response time and accessibility. A solution provider who can use punctual support reduces downtime and maintains manufacturing circulation stable. It's likewise crucial to ask regarding service warranty and service guarantees, check my reference which can show the self-confidence the copyright has in their work.
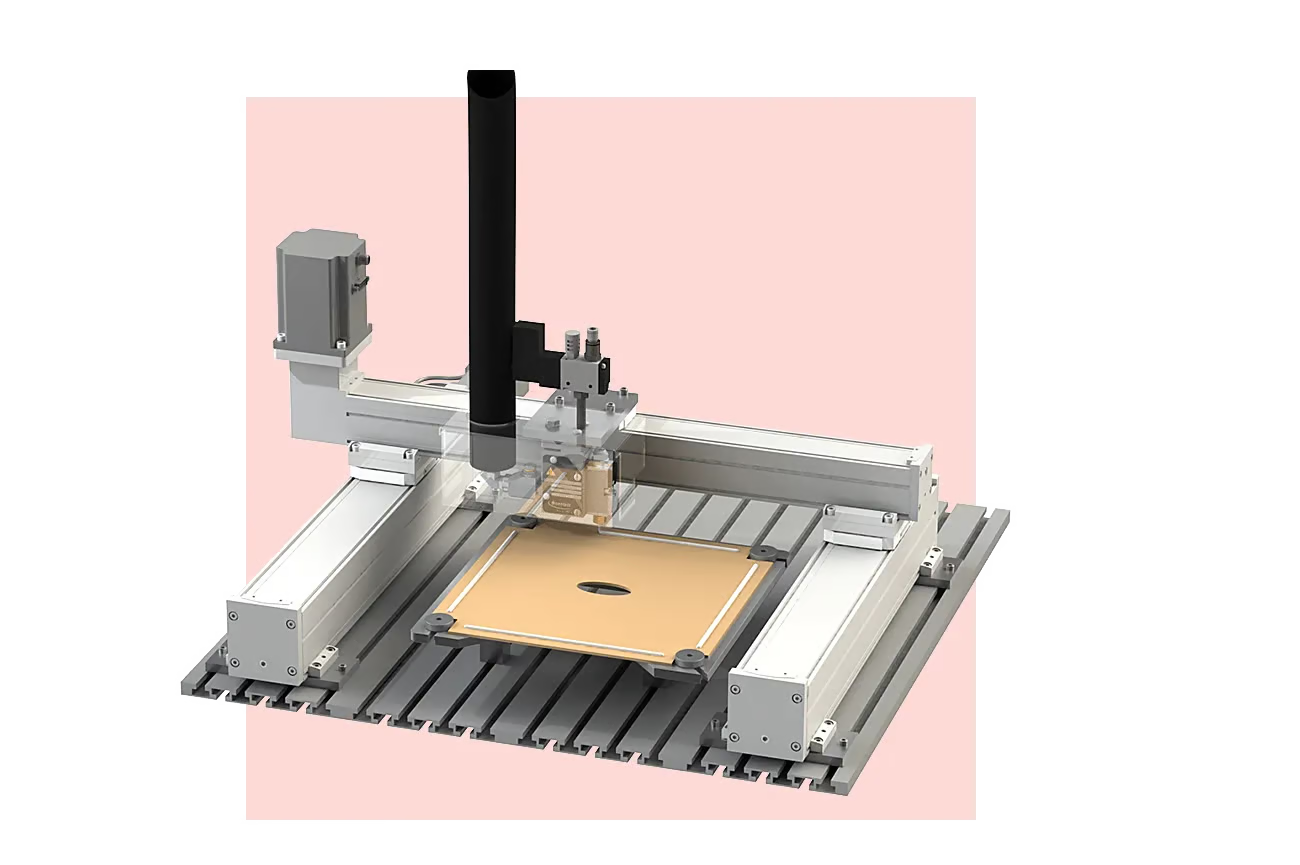
Conclusion
In verdict, the significance of reliable and quick packaging maker fixing services can not be overstated, as they play an important duty in decreasing downtime and ensuring operational effectiveness. Carrying out aggressive upkeep techniques and spending in team training further enhances the longevity of packaging machinery.
Timely repair work of packaging devices are vital for keeping functional performance and lessening downtime.In addition, prompt repair services add to the durability of packaging machinery. In general, the benefits of engaging reliable service carriers expand past instant repair services, positively impacting the entire functional operations of product packaging processes.
Report this page